« `html
Bienvenue dans l’univers fascinant de la fabrication additive hybride.Un consortium de recherche multinational repousse les limites de l’innovation technique.Découvrez comment Ad-Proc-Add II transforme les idées en réalités concrètes.
L’initiative Ad-Proc-Add II incarne une avancée majeure dans le domaine de la fabrication additive. En réunissant des experts d’Autriche, d’Allemagne et de Belgique, le projet vise à optimiser les chaînes de production hybridant méthodes additives et soustractives. Cette collaboration interdisciplinaire favorise l’efficacité des matériaux et l’automatisation numérique.
Au cœur du projet, l’optimisation des chaînes de fabrication additive-soustractive grâce à des processus étroitement intégrés a permis de développer de nouvelles structures de support pour les pièces métalliques imprimées en 3D. Ces structures innovantes réduisent le gaspillage de matériaux et simplifient leur retrait lors des étapes de post-traitement. Testées avec des systèmes de Powder Bed Fusion avec Laser Beam (PBF-LB/M) et de Directed Energy Deposition (DED), ces supports sont ensuite finis par usinage conventionnel, garantissant une qualité supérieure des pièces finales.
Les ingénieurs ont mis au point une base de données de processus qui relie les paramètres géométriques aux propriétés des matériaux et aux spécifications des machines. Cette base permet une planification optimisée des séquences entre les opérations additives et soustractives, améliorant ainsi la fiabilité dimensionnelle des pièces sans nécessiter de multiples itérations de prototypes. De plus, des simulations numériques prédisant la déformation thermique et les contraintes résiduelles ont été développées, offrant une précision accrue dans la prévision de la géométrie finale des pièces.
Pour favoriser l’automatisation, une architecture de planification a été élaborée, connectant les résultats des simulations aux logiciels de génération des trajets d’outil. Cette intégration permet aux systèmes hybrides d’ajuster les stratégies d’usinage en fonction du profil de construction additive, assurant ainsi le respect des tolérances durant les étapes de finition. L’intégration de ces fonctionnalités dans les bases de données de production marque une avancée significative vers des flux de travail manufacturiers fermés et pilotés par les données.
La collaboration industrielle a été essentielle pour garantir la pertinence des recherches dans des environnements de production réels. Des partenaires tels que TU Dortmund, l’Université de Stuttgart et KU Leuven ont travaillé de concert avec des fabricants d’outils, des constructeurs de machines et des développeurs de logiciels pour adapter les solutions aux exigences du marché. Cette synergie a orienté le choix des matériaux, les variables de processus et la fidélité des simulations, assurant ainsi une adoption pratique des innovations développées.
Selon Benjamin Losert, responsable de projet au sein du Mechatronics Cluster d’ecoplus, « Nous constatons déjà un intérêt concret des entreprises souhaitant intégrer nos développements dans leurs systèmes de production. » Les résultats de la recherche ont été présentés lors de conférences telles que EMO, METAV et Formnext, et publiés dans des revues spécialisées. De plus, des ateliers dédiés aux ingénieurs industriels et aux managers techniques ont été organisés pour faciliter l’adoption des outils améliorés et des concepts de fixation développés dans le cadre du projet.
Alors que la fabrication additive hybride n’est pas une nouveauté, son adoption industrielle à grande échelle a été freinée par des interactions de processus imprévisibles, des post-traitements excessifs et des écosystèmes logiciels fragmentés. Ad-Proc-Add II répond à ces défis en liant la géométrie des pièces, les modèles de simulation et la logique d’usinage grâce à des structures de données partagées. Ce flux de travail unifié réduit les approximations, raccourcit les cycles de développement et augmente la reproductibilité de la qualité des pièces, ouvrant la voie à une adoption accrue dans des secteurs exigeants tels que l’aéronautique, l’outillage et le médical.
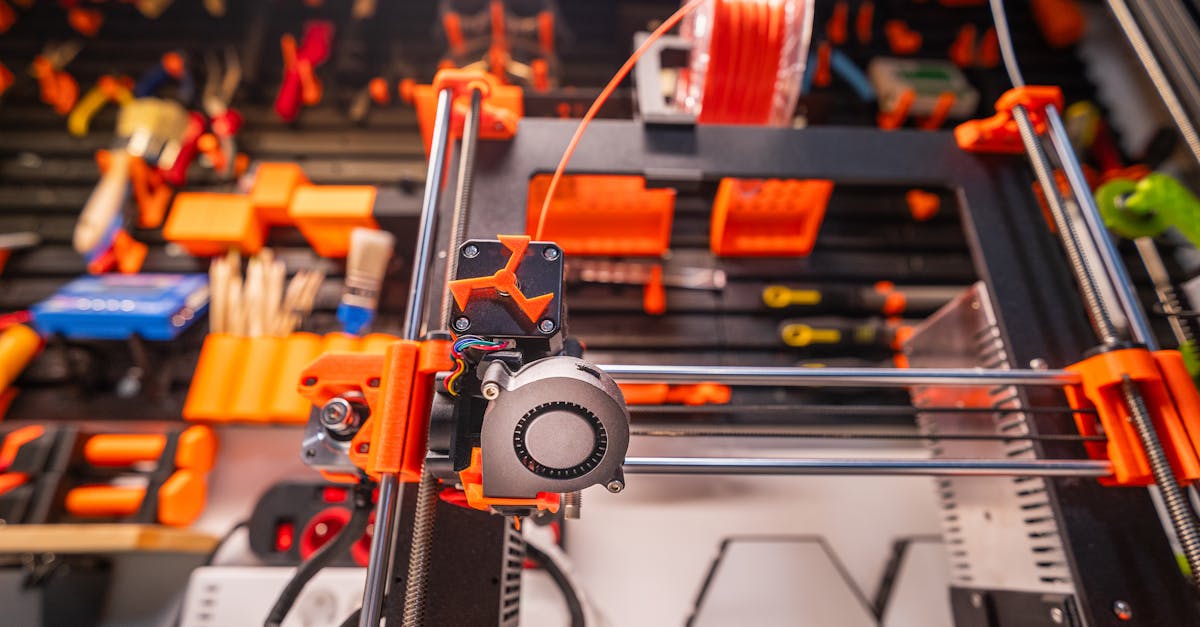
Table of Contents
ToggleAméliorer l’impression 3D hybride grâce à la simulation et à l’automatisation avec ad-proc-add II
La révolution de l’impression 3D continue de transformer l’industrie manufacturière. Grâce au projet Ad-Proc-Add II, une initiative collaborative internationale, l’impression 3D hybride atteint de nouveaux sommets en intégrant la simulation prédictive et l’automatisation digitale. Ce projet, soutenu par des institutions d’Autriche, d’Allemagne et de Belgique, vise à optimiser les chaînes de fabrication additive-soustractive (ASM) pour une efficacité et une précision accrues.
Quels sont les objectifs principaux du projet ad-proc-add II ?
Ad-Proc-Add II, acronyme de Advanced Processing of Additively Manufactured Parts II, a pour objectif de développer des cadres techniques innovants pour la fabrication additive hybride. En se concentrant sur la simulation prédictive, l’efficacité matérielle et l’automatisation numérique, le projet cherche à réduire les déchets de matériaux et à simplifier les étapes de post-traitement. Les chercheurs ont élaboré de nouvelles structures de support pour les pièces métalliques imprimées en 3D, testées via des systèmes de fusion sur lit de poudre au laser (PBF-LB/M) et de dépôt d’énergie dirigée (DED). Ces structures permettent une réduction des déchets et facilitent le retrait des supports lors des processus de finition.
Pour en savoir plus sur les avancées en impression 3D, découvrez l’impression 3D holographique, une technologie émergente utilisant des ondes sonores.
Comment la simulation prédictive renforce-t-elle la fiabilité des pièces imprimées ?
Au cœur d’Ad-Proc-Add II se trouve le développement de simulations numériques capables de prédire les distorsions thermiques, les contraintes résiduelles et la géométrie finale des pièces tout au long des différentes étapes de fabrication. Ces modèles sont validés sur divers alliages métalliques et configurations de machines, garantissant ainsi une fiabilité dimensionnelle accrue sans nécessiter de multiples itérations de prototypes. En simulant la déformation des pièces avant l’impression, les ingénieurs peuvent ajuster les trajets d’outil ou les configurations de support de manière proactive.
Cette approche permet non seulement d’améliorer la fiabilité dimensionnelle, mais aussi de personnaliser précisément les propriétés des composants reconditionnés pour répondre aux exigences de performance préétablies. Par exemple, dans le secteur aéronautique, où la complexité géométrique et les tolérances fonctionnelles sont critiques, ces simulations jouent un rôle crucial.
En quoi l’automatisation digitale optimise-t-elle les processus de fabrication ?
L’automatisation est un pilier essentiel du projet Ad-Proc-Add II. Une architecture de planification a été développée pour connecter les sorties des simulations avec les logiciels de génération de trajets d’outil. Cette intégration permet aux systèmes hybrides d’ajuster automatiquement les stratégies de fraisage en fonction du profil de construction additive, assurant ainsi la préservation des tolérances lors des étapes de finition.
En intégrant ces fonctionnalités dans des bases de données de production, le projet représente une avancée significative vers des flux de travail de fabrication fermés et pilotés par les données. Cette unification réduit les approximations, raccourcit les cycles de développement et augmente la répétabilité de la qualité des pièces. De plus, les méthodes de planification basées sur des bases de données pourraient permettre un déploiement à grande échelle dans des industries telles que l’aérospatiale, l’outillage et le médical.
Pour explorer davantage les innovations en automatisation, visitez l’impression 3D pour assembler des objets dynamiques, une solution avancée pour la création de robots bioniques et de sculptures.
Quelle est l’importance de la collaboration industrielle dans ad-proc-add II ?
Ad-Proc-Add II bénéficie d’une collaboration étroite entre des institutions académiques et des acteurs industriels, garantissant ainsi la pertinence réelle des recherches. Les partenaires incluent l’Institut de Technologie de l’Usinage de TU Dortmund, l’Institut des Machines-Outils de l’Université de Stuttgart, et l’Université KU Leuven, entre autres. Parallèlement, des fabricants d’outils, des constructeurs de machines, des développeurs de logiciels et des utilisateurs industriels finaux ont fourni des retours précieux sur les exigences et les contraintes des environnements de production réels.
Cette synergie entre la recherche et l’industrie a guidé la sélection des matériaux, des variables de processus et la fidélité des simulations. DI Benjamin Losert, responsable de projet au sein du Mechatronics Cluster d’ecoplus, souligne : “Nous observons déjà un intérêt concret de la part des entreprises souhaitant intégrer nos développements dans leurs systèmes de production.”
Les résultats de la recherche ont été présentés lors de conférences renommées telles que EMO, METAV et Formnext, et publiés dans des revues à comité de lecture. De plus, des ateliers spécialisés ont été organisés pour les ingénieurs industriels et les managers techniques, facilitant ainsi l’adoption des nouvelles technologies par les PME grâce au développement d’outils améliorés et de concepts de fixations novateurs.
Quels sont les défis et les opportunités pour l’adoption industrielle de la fabrication additive hybride ?
Bien que la fabrication additive hybride ne soit pas une technique nouvelle, son adoption industrielle généralisée a été freinée par des interactions de processus imprévisibles, un post-traitement excessif et des écosystèmes logiciels disjoints. Ad-Proc-Add II répond à ces défis en liant la géométrie des pièces, les modèles de simulation et la logique d’usinage à travers des structures de données partagées.
Cette workflow unifiée réduit les approximations, raccourcit les cycles de développement, et augmente la répétabilité de la qualité des pièces. Contrairement aux études précédentes qui se concentraient principalement sur l’intégration des machines, Ad-Proc-Add II met l’accent sur l’intelligence des processus. Les méthodes de planification basées sur des bases de données peuvent désormais être déployées à grande échelle dans des secteurs exigeants, tels que l’aérospatiale, l’outillage et le médical.
Pour en savoir plus sur les applications innovantes, consultez l’avenir de la construction militaire avec l’impression 3D en bois massif, une perspective fascinante pour les forces armées.
Quelles sont les perspectives futures pour ad-proc-add II et au-delà ?
Un projet de suivi est en cours de développement pour intégrer davantage les outils de simulation et de planification de données dans les systèmes commerciaux. Cette étape vise à faciliter l’adoption par les industries en fournissant des outils accessibles et performants. Les parties intéressées peuvent demander le rapport technique final en contactant FKM à l’adresse info@fkm.eu, et accéder à une documentation supplémentaire sur le site Ad-Proc-Add II.
Grâce à des innovations continues et une collaboration industrielle renforcée, Ad-Proc-Add II pave la voie vers une fabrication additive hybride plus intelligente et automatisée, capable de répondre aux besoins croissants des industries modernes en matière de précision, d’efficacité et de personnalisation. Pour rester informé des dernières avancées, abonnez-vous à la newsletter de l’industrie de l’impression 3D et découvrez qui a remporté les 3D Printing Industry Awards 2024.
Découvrez également un atelier d’impression 3D pour les adolescents, une initiative qui ouvre un monde créatif à la jeune génération.