3D printing opens up new avenues in many sectors. Digital Light Processing, or DLP, is at the heart of this revolution. Its precision and speed redefine manufacturing standards.
Thanks to the ultra-fine finishing of printing layers, DLP facilitates the creation of biocompatible temporary dental prosthetics. Compared to technologies like SLA or MSLA, DLP printing offers a superior resolution and a consistent quality of produced parts. This guide explores in detail the essential differences between these methods, how they work, and their various applications. By integrating these advancements, the industry harnesses the potential of 3D innovation to meet complex needs.
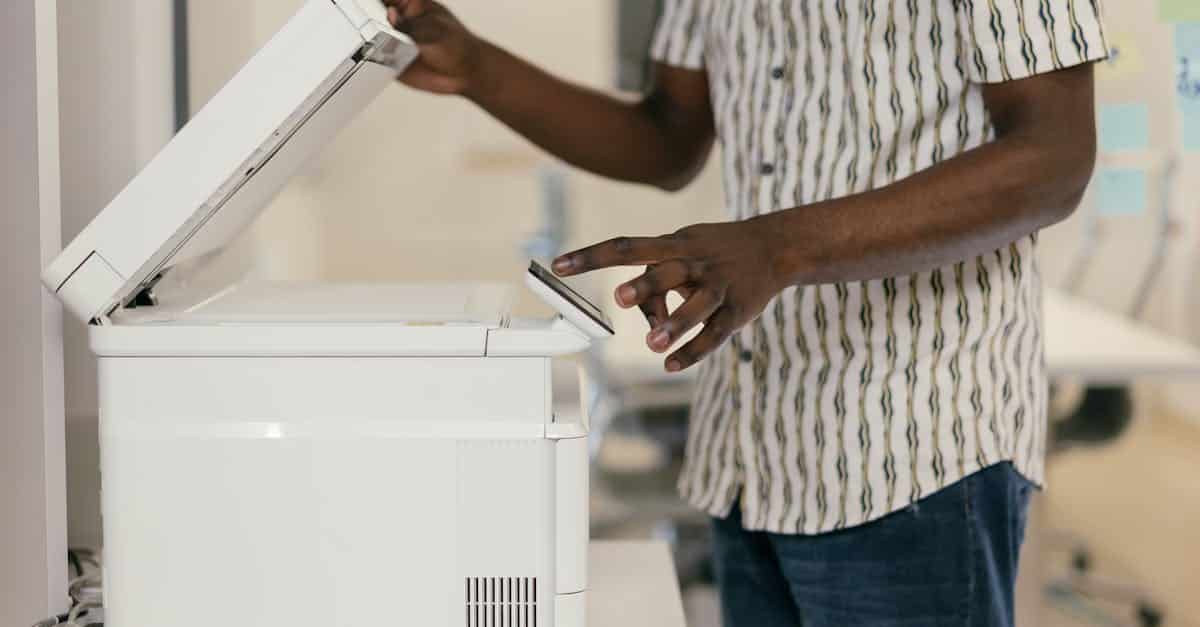
Table of Contents
Toggle3D Printing by Digital Light Processing: A Revolution for Flexible Devices
3D printing by Digital Light Processing (DLP) has transformed many sectors thanks to its ability to produce objects with remarkable precision and speed. Among the most innovative applications are the creation of flexible devices such as actuators, sensors, and energy devices. But how does this technology influence these specific fields, and what are the future implications?
What is 3D Printing by Digital Light Processing and How Does it Work?
DLP 3D printing relies on advanced technology that uses a light source to solidify photopolymer resins layer by layer. Unlike traditional methods such as stereolithography (SLA), DLP projects a complete image of each layer at once using a digital projector. This allows for increased printing speed and high resolution, which is essential for manufacturing complex and precise devices.
The process starts with the preparation of a digital 3D model, typically designed using CAD (Computer-Aided Design) software. This model is then sliced into thin layers, and each layer is projected onto a vat containing the liquid resin. The UV light from the DLP projector polymerizes the resin only in locations corresponding to the pattern of the layer. This cycle is repeated until the desired object is fully created.
The advantages of DLP include not only better resolution and superior surface finish but also greater flexibility in the materials used. This technology allows for the production of complex microscopic structures essential for modern flexible devices.
What are the Advantages of DLP 3D Printing for Flexible Devices?
Flexible devices, such as actuators, sensors, and energy devices, require highly precise and adaptable components. DLP 3D printing perfectly meets these requirements with several major advantages.
First, the high precision of DLP allows for the creation of fine and detailed structures, crucial for the effective operation of sensors and actuators. For instance, in the field of biomedical sensors, increased precision translates to better sensitivity and superior reliability.
Second, the rapid printing speed of DLP significantly reduces production lead times, allowing for quick iteration of prototypes. This accelerates development and innovation, particularly in sectors where time-to-market is a critical factor.
Finally, the durability of the materials used in DLP ensures that manufactured flexible devices are resistant and reliable. Photopolymer resins can be formulated to provide specific mechanical properties tailored to the unique requirements of energy devices, for instance, for flexible batteries or supercapacitors.
How Does DLP 3D Printing Improve the Design of Flexible Actuators?
Flexible actuators are essential components in many applications, ranging from soft robotics to wearable electronics. DLP 3D printing offers unprecedented possibilities for the design and manufacturing of these devices due to its ability to create complex and lightweight structures.
With DLP, it is possible to design actuators with optimized geometries to maximize their efficiency while minimizing the material used. This optimization leads not only to enhanced performance but also to reduced production costs. Additionally, DLP’s flexibility allows for the integration of composite materials, combining for example elastomer resins with reinforced fibers to improve the robustness and flexibility of the actuators.
A concrete example is the manufacturing of flexible actuators used in robotic prosthetics. DLP printing allows for the creation of customized joints and hinges, providing optimal mobility and adaptability tailored to each user.
What are the Challenges and Solutions Associated with DLP 3D Printing for Flexible Sensors?
DLP 3D printing offers many advantages for the production of flexible sensors, but it also has certain challenges. One of the main obstacles is managing the microstructure of the sensors, which requires extreme precision and material uniformity.
Another challenge lies in integrating electronic components into the printed structures. Flexible sensors often need to incorporate conductive circuits, detection elements, and communication systems, necessitating compatibility between the printed materials and electronic components.
To overcome these challenges, research is ongoing to develop special resins compatible with conductive materials and to refine DLP printing processes to enhance the precision and reliability of printed structures. Additionally, advanced post-processing techniques, such as depositing conductive layers after printing, are used to enhance the performance of flexible sensors.
A notable case is that of implantable biomedical sensors, where DLP printing enables the creation of biocompatible and miniaturized devices perfectly suited to stringent medical requirements.
How Does DLP 3D Printing Contribute to Flexible Energy Devices?
Flexible energy devices play a crucial role in the development of wearable technologies and renewable energy systems. DLP 3D printing allows for the manufacture of advanced energy structures with increased efficiency and adaptability.
For example, in the field of flexible batteries, DLP enables the creation of three-dimensional electrodes optimized for better energy density and extended lifespan. DLP’s ability to produce complex structures also promotes the creation of flexible supercapacitors, essential for applications requiring rapid energy release.
Moreover, DLP printing facilitates the integration of energy devices directly into soft structures, such as smart textiles or electronic packaging. This paves the way for innovations such as self-powered clothing and autonomous wearable electronic devices.
A tangible example is the manufacture of flexible solar panels, where DLP enables the production of solar cells with increased efficiency and easy integration into various surfaces, thereby enhancing their applicability in diverse environments.
What are the Future Prospects of DLP 3D Printing in Flexible Devices?
The future of DLP 3D printing in the field of flexible devices looks promising, with ongoing technological advancements and increasing adoption across various industrial sectors. Among the future prospects, we can envision:
- Material Improvement: The development of new photopolymer resins offering advanced mechanical and electrical properties will allow for the creation of even more efficient and specialized devices.
- Multi-Material Integration: The ability to print multiple materials simultaneously will pave the way for multifunctional devices, combining rigidity and flexibility according to the specific needs of each application.
- Automation and Personalization: The automation of DLP printing processes and large-scale customization will enable individual demands to be met with increased efficiency.
- Biomedical Applications: DLP printing will continue to transform the medical sector with the production of custom implantable devices, personalized prosthetics, and advanced surgical tools.
These prospects highlight the immense potential of DLP 3D printing to revolutionize flexible devices, offering innovative solutions tailored to the growing demands of various sectors.
To learn more about integrating multiple properties into a single material through 3D printing, check out this resource. Also discover how 3D printing is shaping the future at Let’s Shape the Future.