Additive manufacturing innovation is revolutionizing the creation of complex materials. With 3D printing, three-dimensional objects and detailed structures take shape layer by layer. This technology opens new doors in the development of flexible and resilient sensors.
3D printed hydrogels, featuring enhanced mechanical and electrical properties, are at the heart of current advances. In particular, their integration into wearable technologies allows for monitoring human movements with unparalleled precision. Methods like bath photopolymerization demonstrate the capability to create robust and adaptable ionic networks. This convergence of materials and technologies paves the way towards innovative health devices.
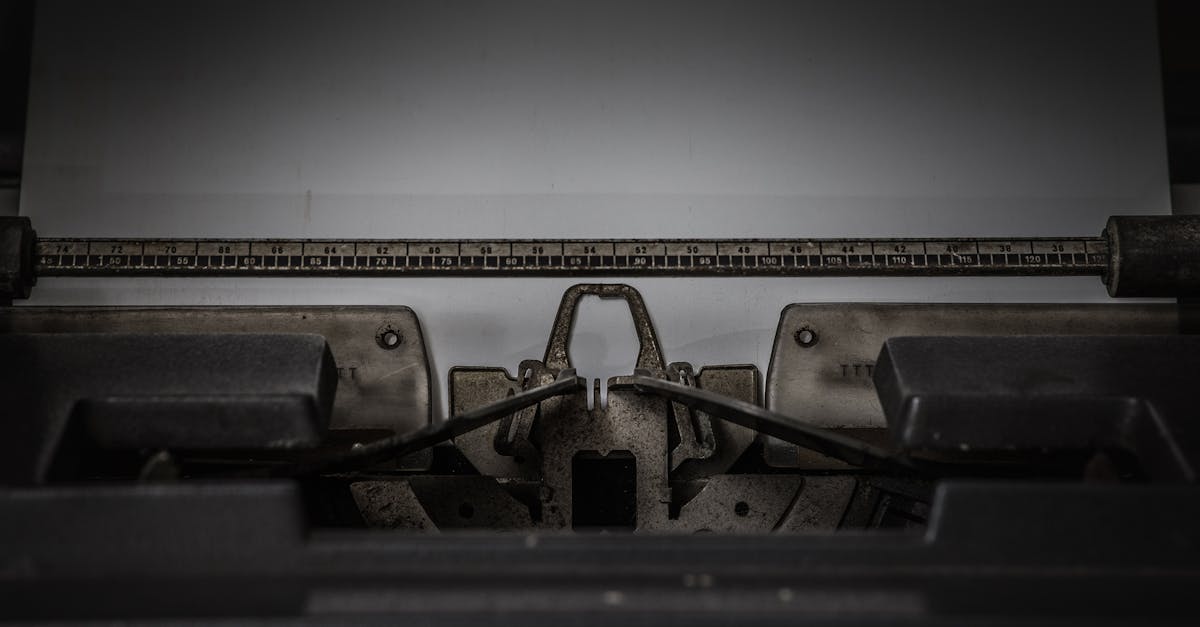
Table of Contents
ToggleIntroduction to 3D Printing of Flexible Hydrogels
3D printing has revolutionized several industries thanks to its ability to create complex objects with unmatched precision. In the field of portable strain sensors, the use of flexible hydrogels made from poly(acrylamide-co-acrylic acid) opens new perspectives for enhancing mechanical and electrical performance. These hydrogels, thanks to their three-dimensional structure, offer flexibility and adaptability that are essential for wearable devices that require high sensitivity and improved robustness.
Poly(acrylamide-co-acrylic acid) is a copolymer that combines the properties of strength and flexibility, making it an ideal candidate for applications in strain sensors. One-step 3D printing enables the efficient fabrication of these hydrogels, thus reducing costs and production time while ensuring consistent quality. This printing method uses UV light photopolymerized resins, allowing for high precision in creating the complex structures required for advanced sensors.
The integration of this technology in the manufacturing of strain sensors offers several advantages. First, it allows for customizing sensors according to the specific needs of users, whether for health monitoring, physical rehabilitation, or human-machine interaction. Furthermore, the hydrogels produced by this method exhibit excellent biocompatibility, which is essential for wearable devices in direct contact with the skin.
Moreover, 3D printing allows for the incorporation of conductive materials directly into hydrogels, thereby enhancing the electrical properties of the sensors. This facilitated integration between flexible materials and electronic components paves the way for more efficient sensors capable of detecting small strains with great accuracy.
To explore the innovation of 3D printing in related fields such as concrete construction, you can check this link.
The Advantages of Poly(acrylamide-co-acrylic acid) in Hydrogels
Poly(acrylamide-co-acrylic acid) is an exceptionally versatile material, widely used in the manufacturing of hydrogels for portable strain sensors. Its copolymer structure provides a unique combination of mechanical and chemical properties, making the hydrogels both robust and flexible. This duality is essential for applications requiring high resistance to mechanical stress while maintaining adequate elasticity to follow human body movements.
Thanks to the presence of acrylic acid groups, this copolymer can form strong ionic bonds, thereby reinforcing the gel structure and increasing its resistance to rupture. These bonds also contribute to better electrical conductivity, which is essential for sensor performance. The addition of polyacrylamide enhances the overall flexibility of the material, allowing the hydrogels to deform under tension without cracking, which is crucial for wearable devices that undergo frequent deformations.
Another major advantage of poly(acrylamide-co-acrylic acid) is its ability to absorb water while maintaining a solid structure. This property is fundamental for hydrogels used in strain sensors, as it allows for effective transduction of mechanical forces into electrical signals. Furthermore, the presence of acrylic acid gives the hydrogel increased sensitivity to pH and ion changes, which can be exploited to enhance sensor accuracy in varied environments.
By integrating this copolymer into the one-step 3D printing process, it is possible to create complex hydrogel structures with remarkable precision. This method allows for fine control over the distribution of components within the gel, thereby optimizing its mechanical and electrical properties. In addition, the produced hydrogels exhibit excellent homogeneity, reducing performance variations between devices.
To learn more about the valorization of food waste in bioinks for 3D printing, explore this article.
The One-Step 3D Printing Process
The one-step 3D printing of flexible hydrogels made from poly(acrylamide-co-acrylic acid) represents a significant advancement in the manufacturing of portable strain sensors. This simplified process allows for a considerable reduction in production time and costs while ensuring high quality and precision of the fabricated devices. Unlike traditional methods that require multiple manufacturing phases, one-step printing integrates all necessary steps, from material preparation to the final creation of the sensor, into a single continuous process.
The process utilizes photopolymerization technologies, where a resin containing the copolymer and other additives is deposited layer by layer under the action of a UV or laser source. This method allows for the rapid creation of complex three-dimensional structures with fine resolution, essential for high precision sensors. Moreover, one-step printing facilitates the integration of functional components directly into the hydrogel, such as conductive electrodes or strain-sensitive matrices.
One key advantage of this process is its ability to customize sensors for specific applications. Whether for medical devices requiring biological compatibility or for sports devices demanding high durability, one-step 3D printing offers the necessary flexibility to adapt the properties of hydrogels according to requirements. This customization is made possible thanks to the ability to modify the resin composition and the printing parameters in real-time, allowing for precise optimization of the mechanical and electrical performances of the sensors.
Furthermore, integrating 3D printing with advanced control technologies enables large-scale production with high consistency. Design data can be rapidly transferred from a digital model to physical production, thus reducing time-to-market for new innovations. This efficiency is reinforced by simulation software that allows predicting and testing the behavior of sensors even before their fabrication, thus ensuring optimal quality of finished products.
To discover the latest recommendations on 3D printing, consult this report.
Enhancements in Mechanical Performance of Strain Sensors
The mechanical performance of strain sensors is a crucial factor for their effectiveness and durability, especially when used in portable applications where they are subjected to constant strains. The use of flexible hydrogels made from poly(acrylamide-co-acrylic acid) through 3D printing allows for significant optimization of these performances. By adjusting the copolymer composition and printing conditions, it is possible to create hydrogel structures that not only withstand repetitive deformations but also maintain their structural integrity over long periods.
The addition of sodium alginate (SA) into the hydrogel network creates additional ionic bonds, thereby reinforcing the gel’s structure and improving its rupture resistance. These flexible bonds contribute to better elasticity, allowing the sensor to return to its original shape after deformation. Moreover, incorporating electrolytes such as sodium chloride (NaCl) into the hydrogel further enhances mechanical properties by creating a double network, combining covalent and ionic bonds that increase the material’s robustness.
Mechanical tests conducted on these hydrogels show a significant improvement in tensile strength and elongation before rupture. These properties are essential for portable sensors that must withstand frequent and varied movements without degrading. For instance, a 3D printed sensor with an optimal amount of NaCl demonstrated superior load-bearing capacity, supporting significant weights without compromising its structure.
Another key innovation is the use of advanced photopolymerization techniques that allow for creating complex geometric patterns within the hydrogel. These patterns not only reinforce the mechanical structure but also improve stress distribution, thereby reducing weak points that could lead to premature ruptures. By optimizing the internal topology of the hydrogel, it is possible to obtain sensors that offer stable and predictable mechanical performance, essential for critical applications such as health monitoring or smart sports devices.
To learn more about the characterization and valorization of hydrolysis charcoal from sewage sludge for 3D printing, visit this article.
Optimization of Electrical Properties of Sensors
In addition to mechanical performance, the electrical properties of strain sensors play a decisive role in their effectiveness and reliability. The flexible hydrogels made from poly(acrylamide-co-acrylic acid) printed in 3D offer unique opportunities to optimize these electrical properties. Electrical conductivity is essential for transducing deformation signals into usable data, thus allowing for precise real-time monitoring of movements.
The integration of electrolytes such as sodium chloride (NaCl) into the hydrogel helps form ionic channels that enhance electrical conductivity. These electrolytes facilitate the movement of ions through the hydrogel network, thereby increasing the sensor’s ability to detect small variations in deformation. Additionally, using appropriate photoinitiators can improve the hydrogel’s electrical stability by ensuring uniform distribution of conducting ions.
Electrical tests conducted on these hydrogels demonstrate a significant improvement in conductivity compared to hydrogels without electrolytes. For example, a hydrogel containing 5% NaCl demonstrated an electrical conductivity greater than 10^-3 S/cm, which is sufficient for effective use in portable strain sensors. This high conductivity allows for rapid and reliable transmission of signals, essential for precise and instantaneous sensor responses.
Moreover, the double network structure formed by covalent and ionic bonds in the hydrogel contributes to better electrical stability under mechanical stress. This means that even when the sensor is stretched or bent, its conductivity remains stable, ensuring consistent performance. This stability is crucial for portable applications where sensors are constantly subjected to repetitive deformations.
Optimizing electrical properties also involves adjusting 3D printing parameters, such as print speed and layer height. These adjustments allow for control over the density of ionic channels in the hydrogel, directly influencing conductivity. Thus, by adjusting these parameters, it is possible to create sensors with conductivity levels tailored to specific requirements, whether high sensitivity or electrical robustness.
To gain further insights on 3D printing recommendations, consult this guide.
Applications of Portable Strain Sensors
Portable strain sensors made from flexible hydrogels based on poly(acrylamide-co-acrylic acid) printed in 3D find a wide range of applications thanks to their enhanced mechanical and electrical performance. These sensors are particularly valued in the fields of health, sport, and rehabilitation, where precise and continuous monitoring of movements is essential.
In the medical sector, these sensors can be used to monitor patient recovery after surgery or injury. They accurately track joint and muscle movements, providing real-time data to healthcare professionals to adjust rehabilitation programs. Furthermore, their flexibility and comfort make them ideal for prolonged use without hindering patients’ natural movements.
Sports applications also benefit from these sensors, particularly in tracking athletic performance and preventing injuries. Strain sensors can be integrated into sports equipment, such as clothing or accessories, to analyze movements and detect areas of excessive tension. This information allows athletes to optimize their technique and reduce the risk of injuries related to repetitive or poorly executed movements.
In the field of soft robotics, these sensors play a crucial role in human-machine interaction. They allow robots to perceive and react to human movements more intuitively and effectively. For example, in exoskeletons designed to assist people with mobility impairments, strain sensors provide precise feedback on user movements, allowing for a more natural and responsive assistance.
Another promising application lies in the realm of advanced user interfaces, where strain sensors can be used to create gesture control devices. These interfaces allow users to control electronic devices, such as computers or smartphones, with simple and intuitive movements, thereby enhancing user experience and paving the way for new forms of interaction.
To explore how the valorization of food losses and waste can contribute to bioinks for 3D printing, visit this article.
Case Studies and Recent Innovations
The integration of flexible hydrogels made from poly(acrylamide-co-acrylic acid) into portable strain sensors has led to several remarkable innovations and case studies illustrating their potential. A recent study conducted by researchers from the Metallurgy and Materials Science Research Institute at Chulalongkorn University demonstrated the efficacy of these hydrogels in health tracking applications. Sensors made from these hydrogels showed high accuracy in detecting joint and muscle movements, providing valuable insights for personalized rehabilitation programs.
Another notable case is the use of these sensors in smart clothing designed for athletes. By integrating the sensors directly into textile fibers, researchers were able to develop garments that track athletic performance and movements in real-time. This technology not only enhances sports performance but also helps to prevent injuries by identifying at-risk movements before they cause harm.
In the field of soft robotics, a development team has integrated these sensors into exoskeletons designed to assist industrial workers. The sensors allow for precise detection of movements and applied forces, providing real-time assistance that adapts to the individual needs of each user. This innovation has improved worker safety and efficiency, reducing fatigue and the risk of injuries related to prolonged physical efforts.
Moreover, researchers have explored the use of these hydrogels in advanced user interfaces, such as contactless gesture control devices. By combining the mechanical and electrical properties of hydrogels, these devices offer increased reactivity and sensitivity, allowing for smoother and more intuitive interactions with electronic devices.
These case studies illustrate not only the versatility of 3D printed flexible hydrogels but also their capacity to transform various industrial sectors. The ongoing evolution of 3D printing techniques and hydrogel formulations promises new innovations that will continue to push the boundaries of portable strain sensors.
To learn more about public recommendations regarding 3D printing, consult this report.
Future Perspectives for 3D Printing of Hydrogels
The future of 3D printing of hydrogels made from poly(acrylamide-co-acrylic acid) looks promising, with technological advances and expanding applications. Researchers continue to explore new hydrogel formulations and innovative printing techniques to further improve the performance of portable strain sensors.
One main direction of future research is the integration of bioactive materials into hydrogels, thus creating sensors with additional functions, such as controlled drug delivery or responsiveness to environmental stimuli. These smart sensors could revolutionize the medical field by offering multifunctional devices capable of simultaneously monitoring and treating various health conditions.
Furthermore, improvements in 3D printing techniques, such as multi-material printing and real-time printing, enable the creation of even more complex and functional hydrogel structures. The use of advanced simulation software could also allow for even finer optimization of the mechanical and electrical properties of hydrogels, paving the way for customized sensors for specific applications.
The rise of artificial intelligence and machine learning also offers new opportunities for the development and optimization of strain sensors. By analyzing the data collected by these sensors, it will be possible to create predictive models that improve the accuracy and responsiveness of devices, making them even more effective for a variety of applications.
Finally, sustainability and ecology will remain important development axes. The use of biopolymers derived from the valorization of food waste, as mentioned in this article, is a promising direction for reducing the environmental footprint of portable strain sensors. These biopolymers offer an ecological alternative to traditional synthetic materials while maintaining high-quality performance.
In conclusion, the potential of 3D printing of flexible hydrogels is immense, with applications extending far beyond portable strain sensors. Ongoing innovations in this field promise to transform not only wearable technologies but also to open new avenues across various industrial sectors.