“`html
Welcome to the fascinating world of hybrid additive manufacturing.A multinational research consortium is pushing the boundaries of technical innovation.Discover how Ad-Proc-Add II transforms ideas into concrete realities.
The Ad-Proc-Add II initiative embodies a major advance in the field of additive manufacturing. By bringing together experts from Austria, Germany, and Belgium, the project aims to optimize production chains by hybridizing additive and subtractive methods. This interdisciplinary collaboration promotes material efficiency and digital automation.
At the heart of the project, the optimization of additive-subtractive manufacturing chains through tightly integrated processes has led to the development of new support structures for 3D printed metal parts. These innovative structures reduce material waste and simplify their removal during post-processing stages. Tested with Powder Bed Fusion with Laser Beam (PBF-LB/M) and Directed Energy Deposition (DED) systems, these supports are then finished by conventional machining, ensuring superior quality of the final parts.
Engineers have developed a process database that connects geometric parameters to material properties and machine specifications. This database allows for optimized planning of sequences between additive and subtractive operations, thus improving the dimensional reliability of parts without requiring multiple iterations of prototypes. In addition, numerical simulations predicting thermal deformation and residual stresses have been developed, providing increased accuracy in predicting the final geometry of parts.
To promote automation, a planning architecture has been developed that connects the results of simulations to tool path generation software. This integration allows hybrid systems to adjust machining strategies based on the additive construction profile, thus ensuring compliance with tolerances during finishing stages. The integration of these features into production databases marks a significant advancement towards closed and data-driven manufacturing workflows.
Industrial collaboration has been essential to ensure the relevance of research in real production environments. Partners such as TU Dortmund, the University of Stuttgart, and KU Leuven have worked closely with tool manufacturers, machine builders, and software developers to tailor solutions to market requirements. This synergy has guided the choice of materials, process variables, and simulation fidelity, thus ensuring a practical adoption of developed innovations.
According to Benjamin Losert, project manager at the Mechatronics Cluster of ecoplus, “We are already seeing concrete interest from companies wishing to integrate our developments into their production systems.” The research results have been presented at conferences such as EMO, METAV, and Formnext, and published in specialized journals. Furthermore, dedicated workshops for industrial engineers and technical managers have been organized to facilitate the adoption of enhanced tools and securing concepts developed within the project.
While hybrid additive manufacturing is not a novelty, its industrial large-scale adoption has been hindered by unpredictable process interactions, excessive post-processing, and fragmented software ecosystems. Ad-Proc-Add II addresses these challenges by linking part geometry, simulation models, and machining logic through shared data structures. This unified workflow reduces approximations, shortens development cycles, and increases the reproducibility of part quality, paving the way for increased adoption in demanding sectors such as aerospace, tooling, and medical.
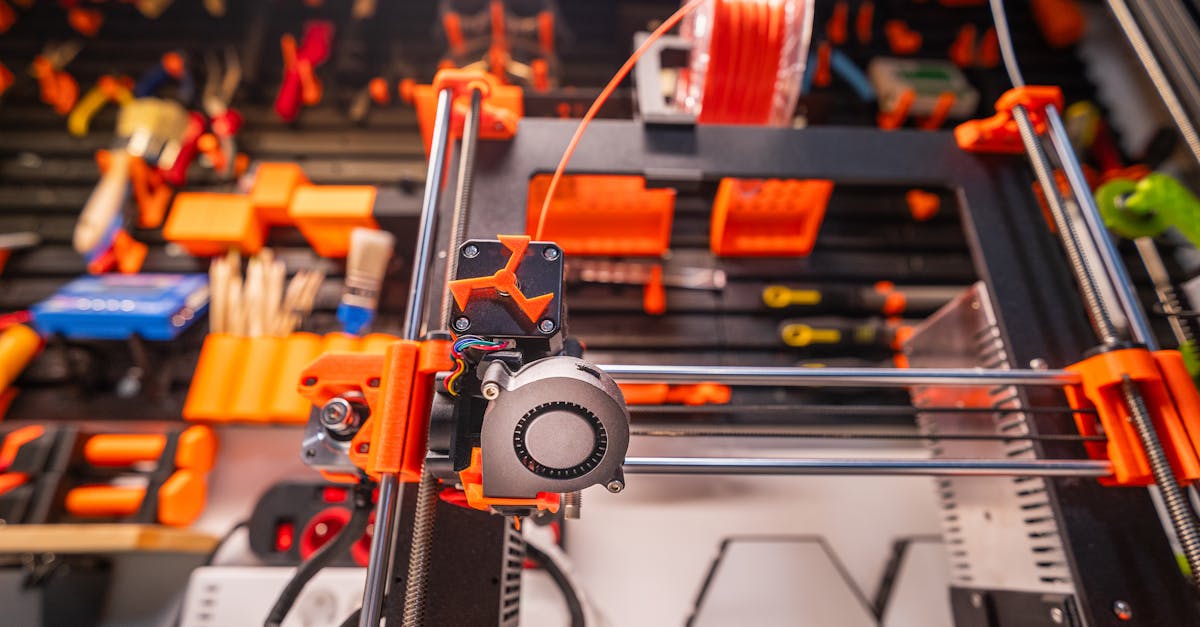
Table of Contents
ToggleImproving hybrid 3D printing through simulation and automation with ad-proc-add II
The 3D printing revolution continues to transform the manufacturing industry. Through the Ad-Proc-Add II project, an international collaborative initiative, hybrid 3D printing is reaching new heights by integrating predictive simulation and digital automation. This project, supported by institutions from Austria, Germany, and Belgium, aims to optimize additive-subtractive manufacturing (ASM) chains for increased efficiency and precision.
What are the main objectives of the ad-proc-add II project?
Ad-Proc-Add II, an acronym for Advanced Processing of Additively Manufactured Parts II, aims to develop innovative technical frameworks for hybrid additive manufacturing. Focusing on predictive simulation, material efficiency, and digital automation, the project seeks to reduce material waste and simplify post-processing steps. Researchers have developed new support structures for 3D printed metal parts, tested via laser powder bed fusion (PBF-LB/M) and directed energy deposition (DED) systems. These structures allow for waste reduction and facilitate the removal of supports during finishing processes.
To learn more about advances in 3D printing, discover holographic 3D printing, an emerging technology using sound waves.
How does predictive simulation enhance the reliability of printed parts?
At the core of Ad-Proc-Add II is the development of numerical simulations capable of predicting thermal distortions, residual stresses, and the final geometry of parts throughout the various stages of manufacturing. These models are validated on various metal alloys and machine configurations, thus ensuring increased dimensional reliability without requiring multiple iterations of prototypes. By simulating deformation of parts before printing, engineers can proactively adjust tool paths or support configurations.
This approach not only improves dimensional reliability, but also precisely customizes the properties of reconditioned components to meet predefined performance requirements. For example, in the aerospace sector, where geometric complexity and functional tolerances are critical, these simulations play a crucial role.
How does digital automation optimize manufacturing processes?
Automation is a fundamental pillar of the Ad-Proc-Add II project. A planning architecture has been developed to connect simulation outputs with tool path generation software. This integration allows hybrid systems to automatically adjust milling strategies according to the additive construction profile, thereby ensuring compliance with tolerances during finishing stages.
By incorporating these features into production databases, the project represents a significant advancement towards closed and data-driven manufacturing workflows. This unification reduces approximations, shortens development cycles, and increases the repeatability of part quality. Furthermore, database-driven planning methods could enable large-scale deployment in industries such as aerospace, tooling, and medical.
To explore further innovations in automation, visit 3D printing to assemble dynamic objects, an advanced solution for creating bionic robots and sculptures.
What is the importance of industrial collaboration in ad-proc-add II?
Ad-Proc-Add II benefits from close collaboration between academic institutions and industrial actors, ensuring the real relevance of research. Partners include the Machining Technology Institute of TU Dortmund, the Machine Tools Institute of the University of Stuttgart, and KU Leuven, among others. Meanwhile, tool manufacturers, machine builders, software developers, and end industrial users have provided valuable feedback on the requirements and constraints of real production environments.
This synergy between research and industry has guided the selection of materials, process variables, and simulation fidelity. Dr. Benjamin Losert, project manager at the Mechatronics Cluster of ecoplus, emphasizes: “We are already observing concrete interest from companies wishing to integrate our developments into their production systems.”
Research results have been presented at renowned conferences such as EMO, METAV, and Formnext, and published in peer-reviewed journals. Additionally, specialized workshops have been organized for industrial engineers and technical managers, thus facilitating the adoption of new technologies by SMEs through the development of enhanced tools and innovative fastening concepts.
What are the challenges and opportunities for the industrial adoption of hybrid additive manufacturing?
Although hybrid additive manufacturing is not a new technique, its widespread industrial adoption has been hindered by unpredictable process interactions, excessive post-processing, and disjointed software ecosystems. Ad-Proc-Add II addresses these challenges by linking part geometry, simulation models, and machining logic through shared data structures.
This unified workflow reduces approximations, shortens development cycles, and increases the repeatability of part quality. Unlike earlier studies that primarily focused on machine integration, Ad-Proc-Add II emphasizes process intelligence. Database-driven planning methods can now be deployed at scale in demanding sectors such as aerospace, tooling, and medical.
To learn more about innovative applications, check out the future of military construction with 3D printing in solid wood, a fascinating prospect for the armed forces.
What are the future perspectives for ad-proc-add II and beyond?
A follow-up project is underway to further integrate simulation and data planning tools into commercial systems. This step aims to facilitate adoption by industries by providing accessible and high-performance tools. Stakeholders can request the final technical report by contacting FKM at info@fkm.eu, and access additional documentation on the Ad-Proc-Add II site.
Through continuous innovations and strengthened industrial collaboration, Ad-Proc-Add II paves the way for a smarter and more automated hybrid additive manufacturing that meets the growing needs of modern industries for precision, efficiency, and customization. To stay informed about the latest advancements, subscribe to the 3D printing industry newsletter and find out who won the 3D Printing Industry Awards 2024.
Also discover a 3D printing workshop for teens, an initiative that opens a creative world to the younger generation.