The integration of additive manufacturing technologies is revolutionizing shipbuilding, especially on American aircraft carriers. The installation of a 3D printed valve collector represents a significant advancement in this field. By combining precision and lightweight design, these components optimize the fluid management systems on board. The use of 3D models paves the way for hyper-personalization of equipment, thus enhancing operational efficiency while minimizing costs.
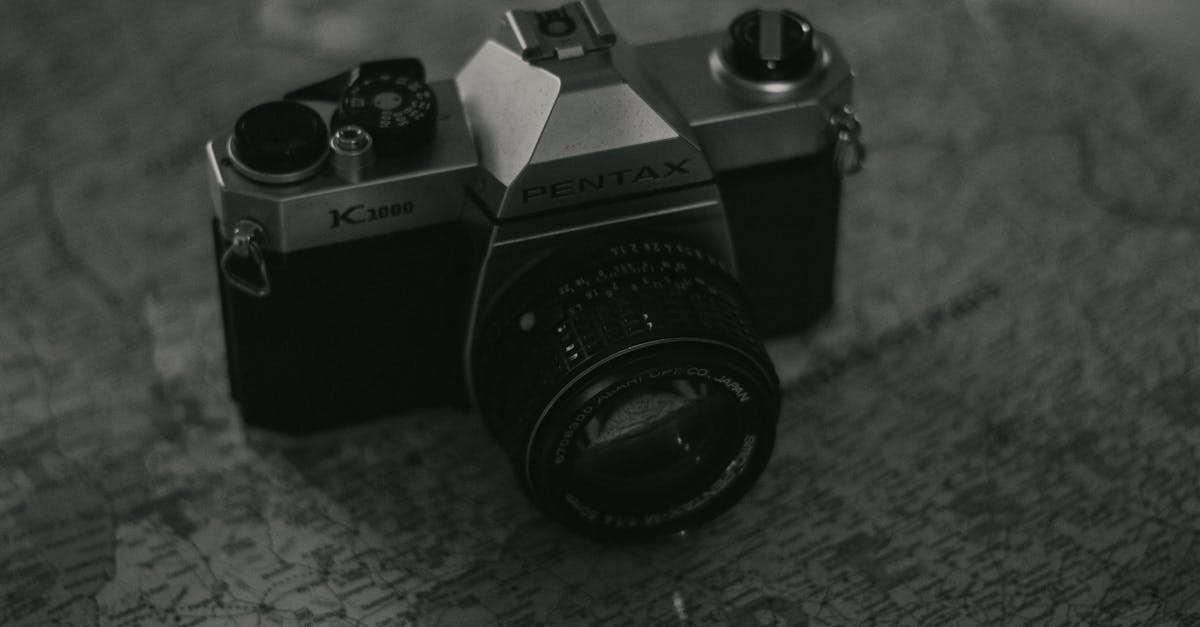
Table of Contents
ToggleInstallation of a 3D Printed Valve Collector
Shipbuilding has always been at the forefront of innovation, and the integration of 3D printed parts in the manufacturing of aircraft carriers is a perfect example of this. The recent initiative by Huntington Ingalls Industries (HII) has demonstrated how modern technologies can transform production methods. The installation of a 3D printed valve collector marks a significant turning point in how components are integrated into these giants of the sea. Not only does this method reduce manufacturing times, but it also allows for customization that precisely meets the specific needs of the armament.
The Advantages of 3D Printed Valve Collectors
Traditional valve collectors require a complex manufacturing process, often associated with high costs and long lead times. 3D printing offers a revolutionary solution to these problems. By using materials such as stainless steel, 3D collectors are not only lightweight but also robust and corrosion-resistant. This method also enables the realization of sophisticated designs that optimize the flow and performance of systems. Furthermore, the environmental impact is reduced through a more efficient use of materials, thus minimizing waste.
The Installation Process on an Aircraft Carrier
Installing a 3D printed valve collector aboard an aircraft carrier requires specific skills in system integration. This begins with a thorough study of design plans to ensure that all parts fit perfectly. The installation team must follow strict protocols to ensure that each component meets the safety and performance standards required by the navy. Thanks to the provided 3D visuals, the integration process becomes more intuitive and less prone to errors.