4D printing is revolutionizing the field of additive manufacturing. Materials capable of transforming in response to their environment open up new perspectives. This technology is inspired by the principles of biomimetics to create dynamic structures.
Researchers from the Technical University of Hamburg and KFUPM are exploring photothermal activation and shape-memory polymers to develop programmable materials. Thanks to machine learning, these materials can undergo complex transformations in response to stimuli such as heat or light. Potential applications include smart packaging, self-assembling components, and advanced medical devices. Despite technical challenges, recent advances offer a promising path towards wider commercial adoption.
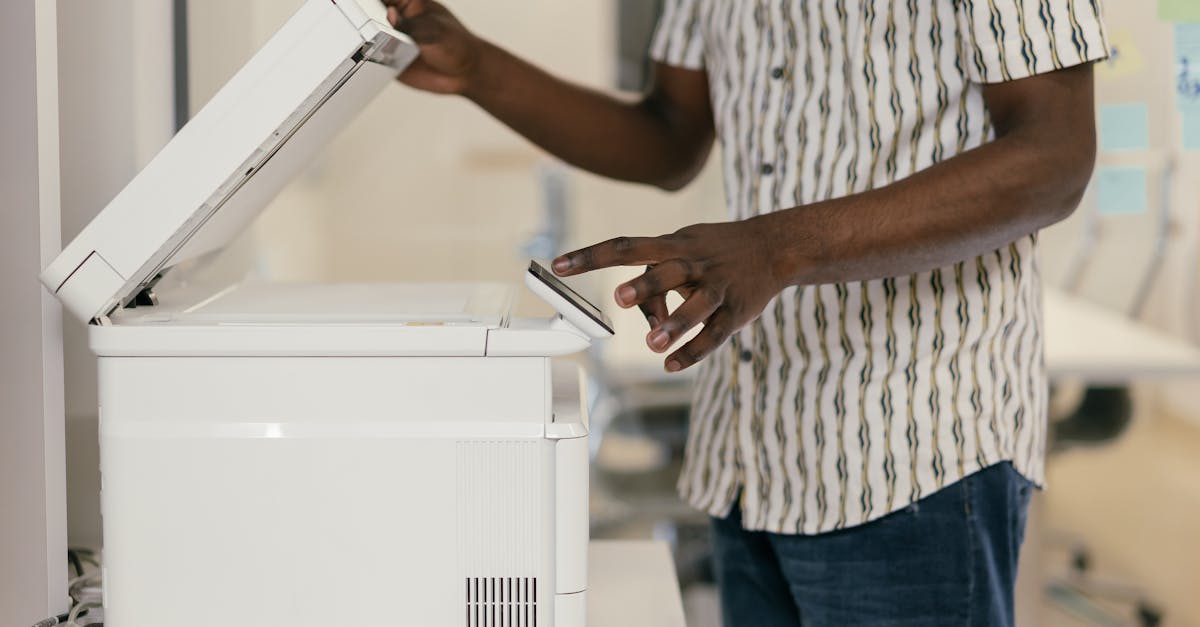
Table of Contents
ToggleWhat is 4D printing and how does it revolutionize reactive materials?
4D printing is an evolution of 3D technology that adds a temporal dimension to the fabricated objects. Unlike traditional 3D printing, which creates static structures, 4D printing allows materials to transform and react to environmental stimuli such as heat, light, or humidity. This ability to change shape or functionality over time opens new opportunities in various sectors, ranging from medicine to aerospace engineering.
The fundamental principle of 4D printing relies on using smart materials, such as shape-memory polymers (SMP), which can memorize a predefined shape and return to it in response to an external stimulus. For example, a structure printed in 4D might automatically unfold when exposed to a certain temperature, without human intervention.
This innovative technology is the result of international collaborative research, such as that conducted by the Technical University of Hamburg and King Fahd University of Petroleum & Minerals (KFUPM). Their study explored photothermal activation and the use of machine learning to create programmable materials capable of dynamic transformations.
By integrating light-absorbing inks onto pre-stretched polymer sheets, researchers were able to design structures that fold in a controlled manner when exposed to light. This process paves the way for applications where flat substrates can transform into complex shapes, thereby enhancing the versatility and efficiency of printed objects.
To learn more about recent advances in 4D printing, check out this article on 3D printing by photopolymerization.
What reactive materials are used in 4D printing?
4D printing relies on a variety of reactive materials capable of responding to environmental stimuli. Among the most commonly used are shape-memory polymers (SMP), hydrogels, liquid crystal elastomers, and magnetic composites.
SMP are particularly prized for their ability to return to a predefined shape after deformation, under the influence of heat or other stimuli. These materials are essential for creating programmable structures that can adapt to their environment.
Hydrogels, on the other hand, are used for their moisture and temperature-sensitive properties, making them ideal for biomedical applications, such as implantable devices or controlled drug delivery systems. Their ability to absorb large amounts of water while remaining flexible makes them useful in demanding environments too.
Liquid crystal elastomers offer a fast and precise response to light stimuli, enabling the creation of dynamic surfaces and structures. These materials find applications in microelectronics and optical devices.
Finally, magnetic composites allow for the manipulation of materials from a distance using magnetic fields, opening the door to innovations in robotics and autonomous transport systems.
To delve deeper into the materials used in 4D printing, visit this article on the impact of organo-mineral scaffolds printed in 3D.
What are the main applications of 4D printing in reactive materials?
4D printing transforms numerous sectors through its reactive materials. Here are some of the most promising applications:
1. Medicine and biomedicine
In the medical field, 4D printed structures can be used to create implantable devices that adapt to the human body. For example, cardiovascular stents that unfold automatically once placed in blood vessels, or orthopedic implants that adjust according to the patient’s needs.
Learn how 4D medicine transforms health for more details.
2. Aerospace and engineering
In the aerospace industry, reactive materials enable the creation of lightweight and adaptive components that can change shape in response to flight conditions. This improves energy efficiency and aircraft performance.
Furthermore, in the civil engineering sector, these materials are used to develop self-healing structures that can adapt and strengthen in response to environmental stresses.
3. Robotics and automation
Adaptive robots significantly benefit from 4D printing. Reactive materials enable robots to modify their shape to perform various tasks, enhancing their flexibility and efficiency.
For example, rehabilitation exoskeletons can adjust their stiffness and support based on the patient’s needs, thus providing a personalized and optimal experience.
4. Smart packaging
The application of reactive materials in 4D printing allows for the development of packaging that can change based on storage conditions. Such packaging can more effectively protect products by adjusting their shape or structure in response to temperature or humidity changes.
This innovation is particularly advantageous for the food and pharmaceutical sectors, where product preservation is crucial.
What challenges does current research need to overcome in 4D printing?
Despite its many promises, 4D printing still faces several technical and scientific challenges to reach its full potential. One of the main obstacles lies in the precise control of transformations of reactive materials. Ensuring that materials react reliably and repetitively to stimuli is essential for guaranteeing the functionality of printed objects.
Moreover, the durability of reactive materials is a major concern. The polymers and other materials used can degrade or lose their properties over time, especially when exposed to variable environmental conditions. Research focuses on developing more robust and fatigue-resistant materials to extend the lifespan of 4D printed objects.
The integration of advanced technologies such as machine learning into the design and manufacturing process also represents a challenge. While using convolutional neural networks and generative adversarial networks offers new possibilities, it is critical to standardize process parameters and improve simulation tools to ensure consistent and predictable results.
Material limitations pose another challenge. Most commercial 3D printing platforms support only a limited number of polymer types, excluding those with harmful emissions, high melting points, or complex rheology. Furthermore, the compatibility of interfaces between different substances remains problematic, risking delamination or crack formation.
Finally, optimizing manufacturing processes to reduce costs and improve efficiency is essential to make 4D printing more accessible and economically viable. Studies like those conducted by Liran ranks second in 3D printing publications among Muslim nations highlight the importance of ongoing research in overcoming these hurdles.
How is machine learning revolutionizing 4D printing?
Machine learning plays a crucial role in the advanced development of 4D printing. By integrating sophisticated algorithms such as convolutional neural networks (CNN) and generative adversarial networks (GAN), researchers can predict and optimize the behaviors of reactive materials even before their fabrication.
Through pre-fabrication prediction models, scientists can simulate the behavior of 4D printed structures under different stimuli. This allows for adjusting design parameters to achieve precise responses tailored to the specific needs of each application.
Inverse design models are particularly innovative. By starting from desired mechanical properties, such as stiffness or stress response, these models calculate the necessary topology of materials to meet these goals. For example, researchers at Northwestern University have developed supervised methods to correlate stiffness values with topological inputs, thus validating the results using advanced simulations.
Moreover, generative algorithms allow navigating through vast design spaces to create complex microstructures while maintaining manufacturability. By encoding microstructure data into compact latent variables via variational autoencoders, researchers can retro-design sophisticated materials with the desired properties.
Advances in machine learning also enhance the reliability and repeatability of 4D printing processes. By anticipating deformations and material behaviors, engineers can optimize printing parameters in real-time, thus reducing errors and increasing the quality of finished products.
To discover more about the impact of machine learning in 4D printing, check out this article on the multifactorial impact of organo-mineral scaffolds in 3D.
What recent advances have marked research in 4D printing?
Recent years have seen significant advances in the field of 4D printing. A collaborative study conducted by the Technical University of Hamburg and the King Fahd University of Petroleum & Minerals (KFUPM) has opened new perspectives by mapping unexplored areas in 4D printing, focusing on photothermal activation and shape-memory polymers (SMP).
One of the key experiments from this study involved printing light-absorbing inks onto pre-stretched polymer sheets. When illuminated, these inks generate heat, causing the material to fold along designated hinges. This method allows flat substrates to transform into complex 3D shapes through uniform light exposure. Researchers emphasized that “this process can be improved by using other absorbers, such as nanoparticles with unique light absorption at specific wavelengths, including those outside the visible spectrum.”
Another notable advance concerns the use of nickel-titanium shape memory alloys (NiTi) in 4D printing through laser powder bed fusion (LPBF). Researchers found that adjusting the laser energy density influenced porosity levels, mechanical consistency, and shape recovery performance. These findings promise significant improvements in tensile strength and fatigue resistance of printed materials.
However, discrepancies persist among studies. Some work highlights cost savings resulting from the elimination of thermal treatments, while others caution that poor process control can lead to increased porosity and reduced mechanical performance. Authors suggest standardizing process parameters, improving simulation tools, and exploring alternative alloys to meet industrial requirements in energy absorption and fatigue durability.
Furthermore, advanced prediction models based on machine learning allow simulating the behavior of printed structures before their fabrication. These models often constrain the design space by using hierarchical microstructure templates or anisotropy-based methods, thus facilitating rapid and efficient optimization of the mechanical properties of composites.
To discover the latest innovations and research results, visit this article on 3D printing publications.
What are the key materials used in 4D printing?
4D printing uses a varied range of reactive materials to enable dynamic transformations. Among the most remarkable are:
- Hydrogels: Primarily used in biomedical applications, these materials can absorb large amounts of water while remaining flexible, making them ideal for implantable devices and drug delivery systems.
- Liquid crystal elastomers: These materials react quickly to light, allowing the creation of dynamic surfaces and structures that can precisely change shape.
- Magnetic composites: Allow for remote manipulation using magnetic fields, opening the door to innovations in robotics and autonomous transport systems.
- Shape-memory polymers (SMP): Capable of returning to a predefined shape after deformation in response to stimuli such as heat, these materials are essential for programmable structures.
Each material has specific advantages that make it suitable for different applications. For instance, hydrogels are perfect for medical uses due to their biological compatibility, while liquid crystal elastomers are ideal for applications requiring rapid and precise responses to light stimuli.
To further explore the mechanisms and applications of multifunctional materials, check out this article on 3D printing by photopolymerization.
What are the advantages and limitations of reactive materials in 4D printing?
The use of reactive materials in 4D printing presents many advantages, but also certain limitations that are crucial to consider.
Advantages
Reactive materials offer unprecedented adaptability, allowing printed objects to transform based on external stimuli. This capability paves the way for innovations in various fields, such as:
- Self-assembly: Creating structures that can automatically assemble themselves, thus reducing the need for human intervention.
- Smart packaging: Developing packaging that can adjust to better protect its contents in response to environmental conditions.
- Adaptive medical devices: Designing implantable devices that can evolve with the human body, thus improving their effectiveness and comfort.
Limitations
Despite their advantages, reactive materials also present some limitations:
- Control of transformations: Ensuring a precise and repeatable reaction to stimuli remains a major challenge, requiring extensive research to improve reliability.
- Durability: Reactive materials may degrade or lose their properties over time, especially when exposed to variable conditions.
- Material compatibility: Interfaces between different reactive materials can cause delamination or cracking issues, thereby compromising the integrity of printed structures.
- Cost and accessibility: Advanced reactive materials can be expensive and difficult to produce in large quantities, thus limiting their commercial adoption.
Despite these challenges, researchers continue to innovate and improve the properties of reactive materials, paving the way for broader adoption of 4D printing across various industries.
What future developments are expected in 4D printing?
The future of 4D printing looks promising with many expected developments. Researchers aim to overcome current challenges by improving the resolution of printers, accelerating prototyping processes, and developing materials with better fatigue resistance.
A key area of development is the integration of artificial intelligence into design and manufacturing processes. Using predictive models based on machine learning will allow for simulating and optimizing the behaviors of reactive materials before their fabrication, thus reducing errors and improving efficiency.
Furthermore, researchers are exploring the use of new alloys and composites that offer better thermal and mechanical compatibility, thus minimizing the risks of printed structure failures. Innovation in printing processes also aims to expand the range of compatible materials, including reactive metals and advanced ceramics.
International and interdisciplinary collaborations will remain crucial to accelerating progress in 4D printing. For instance, joint projects between universities and industries will allow testing and validating new technologies in real-world environments, thereby facilitating their commercial adoption.
To stay informed about the latest advances and discoveries, subscribe to the 3D Printing Industry newsletter.