Les frontières de l’innovation en matériaux sont constamment repoussées par des avancées surprenantes.
Une équipe de chercheurs de l’Université de Houston a récemment dévoilé une méthode révolutionnaire.
En combinant des géométries inspirées de l’origami avec des revêtements élastomères biocompatibles, ils ont créé des structures céramiques flexibles et résistantes.
Cette approche novatrice ouvre la voie à des applications variées, allant des prothèses légères aux composants aérospatiaux capables de résister à des impacts sévères. Grâce à l’utilisation de l’impression 3D, les chercheurs ont pu concevoir des architectures complexes en Miura-ori, renforcées par une couche de polydiméthylsiloxane (PDMS). Les résultats montrent une absorption d’énergie significative et une tolérance accrue aux défaillances, surpassant ainsi les matériaux céramiques traditionnels. Ces avancées prometteuses illustrent le potentiel immense des combinaisons géométriques et de revêtements innovants dans le domaine des matériaux.
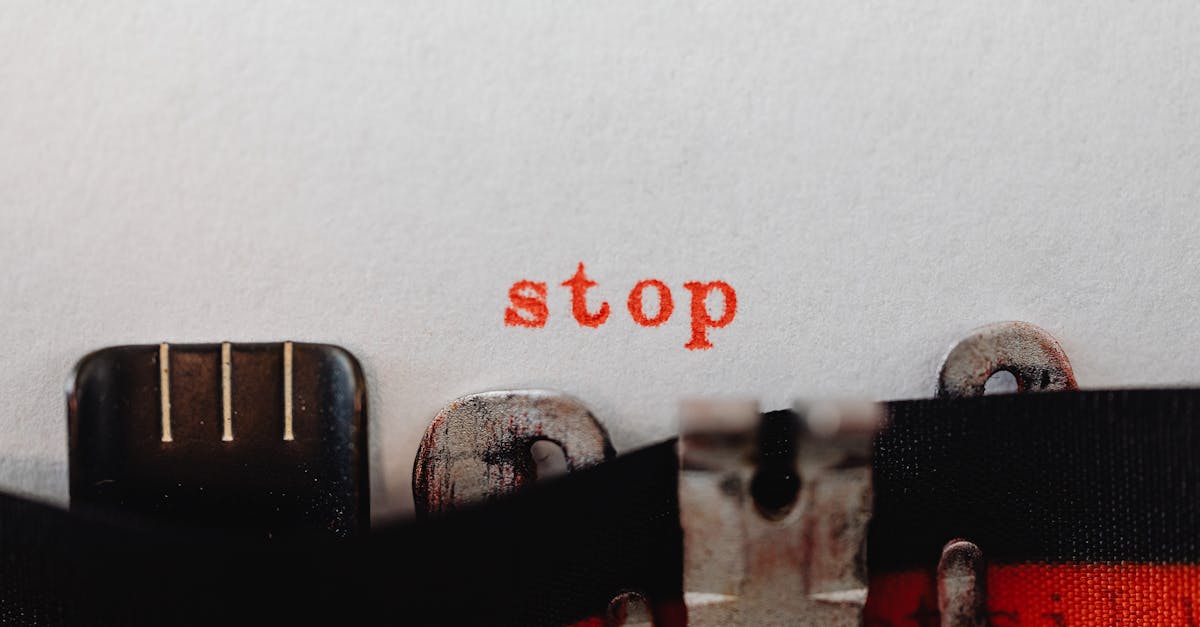
Table of Contents
Togglel’université de houston innove avec des céramiques imprimées en 3d inspirées de l’origami
L’Université de Houston repousse les limites de la technologie en combinant l’impression 3D avec des concepts d’origami pour créer des structures en céramique innovantes. Cette approche révolutionnaire ouvre de nouvelles perspectives dans les domaines biomédicaux et aérospatiaux, où la résistance et la flexibilité des matériaux sont essentielles. En intégrant des géométries inspirées de l’origami avec un revêtement élastomère biocompatible, les chercheurs de l’université ont développé des structures en céramique flexibles et résistantes aux dommages. Cette méthode allie la précision de l’impression 3D et les propriétés uniques des matériaux composites pour offrir des performances exceptionnelles.
comment l’origami influence-t-il la conception des structures en céramique imprimées en 3d?
L’origami, l’art du pliage du papier, sert de source d’inspiration pour la conception de structures en céramique imprimées en 3D à l’Université de Houston. En utilisant des motifs comme le Miura-ori, une technique d’origami connue pour sa capacité à plier et déplier de manière efficace, les chercheurs ont pu créer des architectures céramiques complexes avec des propriétés mécaniques améliorées. Ces géométries permettent de rendre les matériaux traditionnellement fragiles comme la céramique beaucoup plus résistants aux impacts et aux chocs.
Grâce à l’impression 3D, il est possible de réaliser des structures tridimensionnelles avec une grande précision, intégrant des motifs d’origami qui confèrent des caractéristiques telles que la multistabilité, la rigidité ajustable et le comportement auxéthique. Ces propriétés permettent aux structures d’absorber davantage d’énergie et de mieux tolérer les défaillances, rendant les matériaux plus adaptés à des applications exigeantes.
quelles sont les applications potentielles dans le domaine biomédical?
Les structures en céramique flexibles développées par l’Université de Houston présentent un énorme potentiel dans le domaine biomédical. Grâce à leur résistance accrue aux dommages et leur capacité d’absorption d’énergie, ces matériaux peuvent être utilisés pour la fabrication de prothèses, d’implants et d’autres dispositifs médicaux nécessitant à la fois rigidité et flexibilité. Le revêtement en polydiméthylsiloxane (PDMS), un polymère silicone hyperélastique, confère une biocompatibilité essentielle pour les applications implantables, réduisant ainsi les risques de rejet et améliorant la durabilité des dispositifs.
De plus, ces structures peuvent être conçues pour imiter les propriétés du nacre naturel, offrant une combinaison optimale de dureté et de souplesse. Ceci est particulièrement pertinent pour les implants dentaires, orthopédiques et cardiovasculaires, où la compatibilité mécanique avec les tissus biologiques est cruciale. En utilisant des techniques avancées de modélisation et de simulation, les chercheurs peuvent personnaliser les propriétés des structures céramiques pour répondre aux besoins spécifiques de chaque patient, ouvrant ainsi la voie à des solutions médicales personnalisées et innovantes.
en quoi ces céramiques sont-elles bénéfiques pour l’industrie aérospatiale?
Dans le secteur aérospatial, la légèreté et la résilience des matériaux sont des critères essentiels. Les structures en céramique imprimées en 3D par l’Université de Houston répondent parfaitement à ces exigences grâce à leur conception inspirée de l’origami, qui permet une grande rigidité tout en réduisant le poids. Ces matériaux peuvent être utilisés pour la fabrication de composants critiques tels que les panneaux de fuselage, les isolants thermiques et les pièces de pontage aérodynamique.
Le revêtement en PDMS améliore non seulement la flexibilité des céramiques mais aussi leur résistance aux chocs et aux vibrations, deux facteurs courants dans les environnements aérospatiaux. De plus, l’intégration des propriétés auxétiques permet aux structures de mieux absorber et dissiper l’énergie, réduisant ainsi le risque de défaillance catastrophique lors d’événements extrêmes comme les atterrissages brusques ou les impacts de débris spatiaux.
L’utilisation de l’impression 3D permet également une fabrication rapide et personnalisée, essentielle pour les projets aérospatiaux où les délais sont souvent serrés et les exigences techniques élevées. En adoptant ces nouvelles techniques de fabrication, l’industrie aérospatiale peut bénéficier de composants plus performants, allégés et durables, contribuant ainsi à une meilleure efficacité énergétique et à des performances globales améliorées des aéronefs et des engins spatiaux.
comment les chercheurs ont-ils testé la performance des structures en céramique?
Les performances des structures en céramique développées par l’Université de Houston ont été rigoureusement évaluées à travers une série de tests mécaniques et de simulations avancées. Les chercheurs ont réalisé des tests de compression dans trois directions orthogonales en utilisant un système Instron ElectroPuls E3000. Ces tests ont révélé que les céramiques non revêtues échouaient de manière catastrophique à de faibles déformations, particulièrement dans leur axe de faiblesse. En revanche, les échantillons revêtus de PDMS ont montré une absorption d’énergie significativement plus élevée avant la défaillance, démontrant une amélioration notable de la ténacité.
L’utilisation de la microscopie électronique à balayage (SEM) a permis de visualiser l’effet du revêtement PDMS sur la propagation des fissures. Les images SEM ont montré que le revêtement interrompait ou ralentissait la croissance des fissures, conduisant à une défaillance localisée et progressive plutôt qu’à un effondrement soudain. Cette observation a été confirmée par les images optiques prises à différents stades de la compression, où les structures revêtues ont maintenu leur intégrité structurale même sous des contraintes dévastatrices pour les échantillons non revêtus.
De plus, des simulations par éléments finis utilisant ABAQUS/Explicit ont été effectuées pour modéliser le comportement des structures sous charge. Ces simulations, basées sur des modèles matériels adaptés pour la céramique et le PDMS, ont parfaitement concordé avec les résultats expérimentaux, montrant une redistribution des contraintes et une accumulation de dommages retardée dans les échantillons revêtus. Cette combinaison de tests expérimentaux et de simulations informatiques assure une compréhension approfondie des propriétés mécaniques des nouvelles structures en céramique, validant ainsi leur potentiel pour des applications exigeantes.
quel est le processus de fabrication des structures en céramique Miura-ori?
Le processus de fabrication des structures en céramique Miura-ori développé par l’Université de Houston repose sur une combinaison innovante de stéréolithographie à base de boue et de techniques d’impression 3D. Tout commence par la conception numérique des structures en utilisant des logiciels de modélisation tels que MATLAB et SolidWorks, permettant d’optimiser les paramètres des unités Miura-ori pour s’assurer que les dimensions finales seront précises après la sintering thermique.
La stéréolithographie à base de boue utilise une résine remplie de silice et exposée à la lumière ultraviolette pour construire des formes complexes avec une haute résolution. Cette méthode permet de créer des géométries d’origami détaillées, spécialement conçues pour exploiter les avantages mécaniques tels que la multistabilité et le comportement auxétique. Après l’impression, les composants passent par un processus de nettoyage et de séchage avant d’être soumis à une sintering thermique multi-étapes à des températures allant jusqu’à 1271 °C. Cette étape cruciale élimine le liant polymère et fusionne les particules de silice, aboutissant à une céramique dense capable de supporter des charges élevées avec une densité finale d’environ 50 %.
Pour garantir la précision dimensionnelle malgré le rétrécissement induit par la sintering, les fichiers de conception numérique sont ajustés en amont. Une microscopie électronique à balayage (SEM) est utilisée pour vérifier la densification réussie et le développement des joints de grains au sein de la structure céramique achevée. Ce processus de fabrication méticuleux permet de produire des structures en céramique non seulement robustes mais aussi flexibles et adaptées à des applications spécifiques nécessitant des performances mécaniques élevées.
quels sont les bénéfices du revêtement en polydiméthylsiloxane (PDMS)?
Le polydiméthylsiloxane (PDMS) joue un rôle crucial dans l’amélioration des propriétés des structures en céramique de l’Université de Houston. Ce polymère silicone hyperélastique est appliqué en tant que revêtement élastomère sur les structures céramiques, conférant une flexibilité exceptionnelle tout en maintenant la rigidité nécessaire pour des applications structurales. Le processus de dip-coating assisté par vide permet une application uniforme du PDMS, garantissant une épaisseur constante de 75 à 100 microns qui couvre toutes les surfaces et les plis de la structure sans infiltrer le cœur de la céramique.
L’intégration du PDMS apporte plusieurs avantages notables. Premièrement, il améliore considérablement l’absorption d’énergie des structures céramiques, leur permettant de résister à des impacts et des déformations sans s’effondrer. Deuxièmement, le revêtement empêche la propagation rapide des fissures, ce qui conduit à une défaillance localisée plutôt qu’à une rupture catastrophique. Cette protection supplémentaire est particulièrement bénéfique dans des applications où la sécurité et la fiabilité sont primordiales, telles que les implants biomédicaux et les composants aérospatiaux.
De plus, le PDMS confère une biocompatibilité essentielle pour les applications médicales, réduisant le risque de rejet et améliorant l’intégration des implants avec les tissus biologiques. Sur le plan mécanique, le revêtement améliore la ténacité des structures en céramique, rendant les matériaux plus durables et résistants aux cycles répétés de charge et de décharge, comme le montrent les tests de chargement cyclique réalisés par l’équipe de recherche.
comment les simulations ont-elles validé les résultats expérimentaux?
Les simulations informatiques ont été essentielles pour valider les résultats expérimentaux obtenus par l’Université de Houston. En utilisant le logiciel ABAQUS/Explicit, les chercheurs ont créé des modèles par éléments finis qui intègrent des modèles matériels spécifiques pour la céramique et le PDMS. Le modèle pour la céramique repose sur la plasticité endommagée en béton, tandis que le PDMS est modélisé selon le modèle d’Arruda–Boyce, adapté pour capturer son comportement hyperélastique.
Les simulations ont permis d’observer la distribution des contraintes et l’accumulation de dommages au sein des structures sous charge. Les résultats ont montré que les échantillons revêtus de PDMS présentaient des concentrations de contraintes réduites et une accumulation de dommages retardée par rapport aux échantillons non revêtus. De plus, les routines de suppression d’éléments utilisées dans le modèle ont facilité la simulation réaliste de la fracture et de la séparation des matériaux, reflétant fidèlement les défaillances observées lors des tests expérimentaux.
L’exactitude des simulations a été confirmée par la convergence du maillage, avec les modèles finaux comportant près de 300 000 éléments pour assurer une stabilité numérique. Cette correspondance étroite entre les simulations et les tests réels renforce la confiance dans le modèle utilisé et offre une base solide pour prédire le comportement des structures en céramique dans diverses conditions de charge. De plus, les simulations ont fourni des insights supplémentaires sur l’évolution des dommages au fil du temps, permettant aux chercheurs de mieux comprendre les mécanismes de défaillance et d’optimiser les conceptions futures.
quelles sont les avancées futures prévues par l’équipe de recherche?
L’équipe de recherche de l’Université de Houston envisage de poursuivre l’optimisation des paramètres des cellules unitaires Miura-ori en utilisant des techniques de conception algorithmique et de simulation avancée. Les futurs travaux viseront à maximiser les performances des structures en fonction des conditions de charge spécifiques à chaque application, qu’elles soient biomédicales ou aérospatiales.
L’utilisation de méthodes d’optimisation avancées, telles que les méthodes bayésiennes ou les algorithmes génétiques, devrait permettre l’identification rapide des configurations de design optimales pour relever de nouveaux défis en ingénierie. Ces techniques permettront de parcourir efficacement l’espace de conception pour trouver des solutions innovantes qui allient légèreté, robustesse et flexibilité des matériaux.
Par ailleurs, l’équipe prévoit d’explorer de nouvelles combinaisons de matériaux et de revêtements pour améliorer encore les propriétés des structures en céramique. L’intégration de matériaux réactifs ou de composites hybrides pourrait ouvrir la voie à des applications encore plus diversifiées, allant des dispositifs médicaux intelligents aux composants aérodynamiques adaptatifs.
En outre, les chercheurs souhaitent collaborer avec des partenaires industriels pour tester et appliquer ces nouvelles structures dans des environnements réels, recueillant ainsi des données pratiques pour affiner davantage leurs conceptions. Ces efforts devraient non seulement renforcer la position de l’Université de Houston en tant que leader dans le domaine de l’innovation en matériaux, mais aussi contribuer à des avancées significatives dans les technologies biomédicales et aérospatiales.
Pour en savoir plus sur les défis rencontrés dans l’adoption de l’impression 3D dans l’industrie aérospatiale, consultez ce lien.
comment ces innovations s’inscrivent-elles dans les tendances actuelles de l’impression 3d?
Les innovations de l’Université de Houston s’inscrivent parfaitement dans les tendances actuelles de l’impression 3D, qui vise à développer des matériaux plus performants et des méthodes de fabrication plus efficaces. L’intégration de concepts d’origami dans les structures imprimées en 3D reflète une tendance croissante à tirer parti des principes de la nature et des arts traditionnels pour résoudre des problèmes modernes en ingénierie.
La conception inspirée de l’origami permet non seulement de créer des structures plus légères et plus résistantes, mais elle offre aussi une flexibilité de conception inégalée, essentielle pour les applications complexes. L’adoption de matériaux composites, comme la céramique combinée avec le PDMS, rejoint également la tendance vers l’utilisation de matériaux hybrides pour optimiser les propriétés mécaniques et fonctionnelles des objets imprimés.
De plus, le recours à des méthodes de simulation avancées et à des algorithmes d’optimisation place ces innovations au cœur de la transition vers une fabrication intelligente et adaptative. Ces approches permettent non seulement de réduire les cycles de développement, mais aussi d’améliorer la précision et la fiabilité des structures produites, répondant ainsi aux exigences croissantes des secteurs biomédical et aérospatial.
Ces avancées démontrent également l’importance de la collaboration interdisciplinaire, combinant des connaissances en mécanique, en matériaux, en biocompatibilité et en conception algorithmique pour créer des solutions holistiques et innovantes. Cela réaffirme le rôle central de l’Université de Houston dans la conduite de recherches de pointe et dans la propulsion des technologies d’impression 3D vers de nouveaux sommets.
Pour découvrir comment une encre céramique imprimée en 3D pourrait contribuer à la protection de notre planète en sauvant l’eau, consultez ce lien.
quels sont les défis à surmonter pour la commercialisation de ces structures?
Bien que les innovations de l’Université de Houston représentent des avancées significatives, plusieurs défis subsistent avant que ces structures en céramique imprimées en 3D puissent être commercialisées à grande échelle. L’un des principaux obstacles est la réduction des coûts de production associés aux méthodes d’impression 3D et aux matériaux utilisés. L’impression de structures complexes comme le Miura-ori demande des équipements spécialisés et des matériaux coûteux, ce qui peut limiter la rentabilité à court terme.
Un autre défi majeur est la standardisation des processus de fabrication. Pour que ces structures puissent être adoptées par l’industrie, il est essentiel de développer des protocoles de production fiables et reproductibles. Cela inclut la maîtrise des étapes de sintering thermique, du revêtement en PDMS et de l’ajustement des conceptions numériques pour compenser le rétrécissement post-sintering.
La réglementation et la certification constituent également des barrières importantes, particulièrement pour les applications biomédicales où la conformité aux normes de sécurité et de biocompatibilité est stricte. Obtenir les approbations nécessaires exige des tests approfondis et des études cliniques, processus qui sont longs et coûteux.
Enfin, il existe un besoin de collaboration interdisciplinaire pour surmonter ces défis. Cela implique de travailler en étroite collaboration avec des partenaires industriels, des organismes de réglementation et des experts en matériaux pour affiner les technologies et assurer leur adéquation aux exigences du marché. En investissant dans la recherche continue et en établissant des partenariats stratégiques, l’Université de Houston peut surmonter ces obstacles et accélérer la commercialisation de ses innovations.
Pour en savoir plus sur les avancées de l’impression 3D de nouvelle génération exploitant l’énergie de fusion, visitez ce lien.
quelles collaborations renforcent ce projet de recherche?
Le succès des projets de recherche menés par l’Université de Houston repose en grande partie sur des collaborations étroites avec divers partenaires académiques, industriels et gouvernementaux. Ces alliances permettent de partager des connaissances, des ressources et des infrastructures, accélérant ainsi le développement et la mise en œuvre des innovations technologiques. Les partenariats avec d’autres institutions universitaires offrent un enrichissement académique et scientifique, permettant d’exploiter une expertise multidisciplinaire essentielle pour des projets aussi complexes.
De plus, des collaborations avec des industries clés des secteurs biomédical et aérospatial sont cruciales pour adapter les technologies développées aux besoins réels du marché. Ces partenariats facilitent également le transfert technologique, transformant les découvertes de laboratoire en produits commerciaux viables. Par exemple, travailler avec des fabricants d’implants médicaux ou des constructeurs aérospatiaux permet de tester et d’optimiser les structures céramiques dans des conditions d’utilisation réelles.
Les liens avec des organismes gouvernementaux et des laboratoires de recherche de pointe offrent également un soutien financier et logistique indispensable. En outre, ces collaborations encouragent l’innovation ouverte et l’échange d’idées, qui sont essentiels pour repousser les frontières de la recherche et développer des solutions novatrices qui répondent aux défis actuels et futurs.
En soutenant ces collaborations multiples et variées, l’Université de Houston assure que ses recherches en céramiques imprimées en 3D sont non seulement scientifiquement rigoureuses mais également alignées sur les besoins et les attentes de l’industrie et de la société.
Pour explorer davantage les nouvelles frontières des matériaux réactifs dans l’impression 4D, consultez ce lien.
quels sont les retours des experts sur cette innovation?
Les innovations de l’Université de Houston ont suscité un vif intérêt et reçu des retours positifs de la part des experts dans les domaines des matériaux avancés et de l’ingénierie. Les publications scientifiques, notamment celles publiées dans la revue Advanced Composites and Hybrid Materials, ont été saluées pour leur rigueur méthodologique et la profondeur des analyses présentées. Les experts reconnaissent la contribution significative de cette recherche à l’avancement des technologies de fabrication additive et à l’amélioration des performances des matériaux céramiques.
Les chercheurs
Maksud Rahman et Md Shajedul Hoque Thakur, leaders du projet, ont été félicités pour leur approche innovante combinant origami et impression 3D, ouvrant de nouvelles avenues pour la conception de matériaux composites. Leur capacité à maîtriser des procédés complexes tels que la sintering thermique et le dip-coating assistant par vide a été particulièrement appréciée, démontrant une expertise profonde dans la fabrication et le traitement des matériaux avancés.
De plus, les simulations par éléments finis ont été soulignées comme une étape clé dans la validation des performances des structures, offrant une compréhension détaillée des mécanismes de résistance et de défaillance. Les experts ont également noté l’importance des collaborations interdisciplinaires et industrielles mises en place par l’équipe de recherche, considérant cela comme un modèle pour les futurs projets innovants.
En somme, cette innovation est perçue comme un pas important vers la réalisation de matériaux plus performants, adaptables et durables, avec des implications majeures pour des secteurs critiques tels que la biomédecine et l’aérospatiale. Les retours encourageants des experts renforcent la crédibilité et le potentiel commercial des recherches menées par l’Université de Houston, promettant des avancées continues et des applications pratiques dans un avenir proche.
comment suivre les dernières avancées de cette recherche?
Pour rester informé des dernières avancées concernant les structures en céramique imprimées en 3D à l’aide de l’origami et d’autres innovations de l’Université de Houston, il est recommandé de s’abonner à des sources d’informations spécialisées et de suivre les publications académiques pertinentes. La newsletter de 3D Printing Industry est une excellente ressource pour obtenir des mises à jour régulières, des analyses approfondies et des insights exclusifs sur les développements les plus récents dans le domaine de l’impression 3D et des matériaux avancés.
De plus, consulter régulièrement des articles et des études de cas publiés dans des revues scientifiques renommées permet de se tenir au courant des nouvelles découvertes et des applications potentielles des technologies de fabrication additive. Participer à des conférences et des symposiums spécialisés, ainsi qu’à des webinaires organisés par des institutions académiques et des leaders industriels, offre également des opportunités précieuses pour apprendre directement des chercheurs et des praticiens du secteur.
Pour découvrir l’impact des innovations en impression 3D sur la fabrication des antennes spatiales, visitez ce lien.
Enfin, pour une veille continue sur les défis et les opportunités dans l’adoption de l’impression 3D, ainsi que pour explorer comment des solutions innovantes comme celles développées par l’Université de Houston peuvent transformer diverses industries, n’hésitez pas à explorer les différentes ressources et articles disponibles sur des plateformes spécialisées telles que Build Future Now.